A complete guide to replacing ceramic floor tiles without destroying the subfloor.
Replacing ceramic floor tiles does not always mean destroying the old tiles and rebuilding the subfloor. There are new methods that allow for the installation of new tiles without having to remove the old flooring. These methods reduce costs, time, and environmental pollution, and are especially useful in residential, office, and commercial buildings where there is no possibility of creating noise and dust.
In this article, we will examine new solutions for replacing ceramics without destruction, their advantages and disadvantages, the tools required, and the steps to implement them step by step.
Can ceramic floor tiles be replaced without destroying them?
Many people have concerns when deciding to replace ceramic floor tiles, such as damage, dust, high costs, and long installation times. The traditional idea is that to replace flooring, you first have to destroy the old ceramic tiles and then lay a new subfloor. However, today, methods have been invented that do not require destruction.
In these methods, the new ceramic is installed directly on the old flooring. This technique not only reduces demolition and subflooring costs, but also speeds up the project. In addition, there is no need to remove construction debris, which is a great advantage for renovation projects.
Below, we will examine the various methods that can be used to replace ceramics without destruction.
Old methods of replacing ceramic floors and their problems
Traditional ceramic replacement methods usually include the following steps:
- Demolition and removal of old ceramics
- Leveling and leveling the subsurface
- Applying new adhesive or mortar
- Installing new ceramics
- Final tying and cleaning
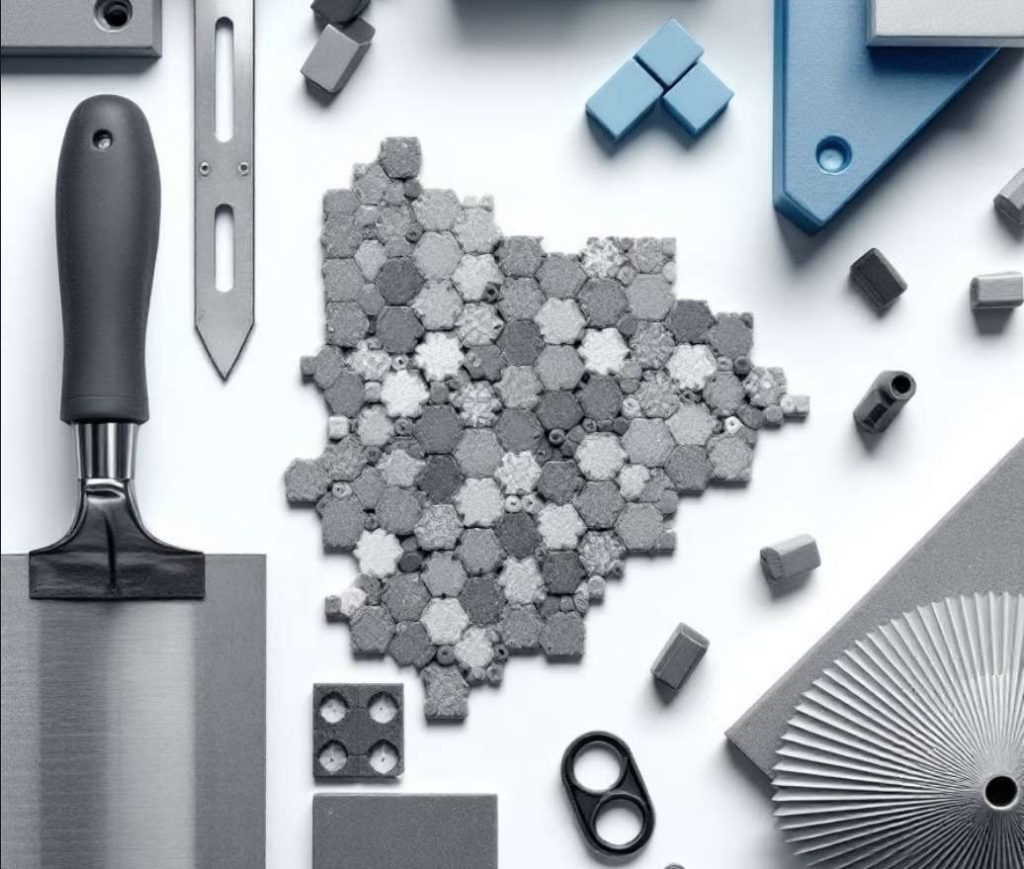
Problems with the traditional method
- ✅ High costs: In addition to the cost of purchasing new ceramics, demolition, foundation, and labor costs are also added to the project costs.
- ✅ Long implementation time: Due to the multiple steps, the project may take several days or even weeks.
- ✅ Pollution and dust: The destruction of old ceramics creates a lot of dust, which can be problematic for the building’s residents.
- ✅ Damage to underlying layers: In some cases, removing old ceramics can damage the underlying surface and increase the need for additional repairs.
Due to these problems, new methods for replacing ceramics without the need for destruction have been considered, which we will introduce below.
New methods of replacing ceramics without destruction: comparison and introduction
New methods that allow for the installation of new flooring without destroying old ceramics include the following:
1- Using special tile adhesives on tiles
In this method, powerful adhesives designed to bond tile to tile are applied to the old ceramic and the new ceramic is placed on top of it.
Advantages:
- Quick implementation without the need for demolition
- Reducing labor and material costs
- No dust or environmental pollution
Disadvantages:
- Slight increase in floor height
- Need to check the adhesion of old ceramic before installation
2- Using ultra-thin ceramics
These types of ceramics have a very small thickness (about 3 to 6 mm) and are easily installed over old ceramics.
Advantages:
- Prevent excessive floor height increase
- Quick implementation without the need to change doors and cornices
Disadvantages:
- Higher price than conventional ceramics
3- Using epoxy flooring
This type of flooring requires no adhesive and can be applied directly over old ceramics.
Advantages:
- Variety of colors and designs
- Fast installation and low cost
Disadvantages:
- Less durable than real ceramic
4- Advantages and disadvantages of replacing ceramics without the need for demolition
Advantages:
- Reduce execution time
- Reducing overall costs
- No need to destroy or create dust
- Easy to implement even in residential and office spaces
Disadvantages:
- Increasing floor height (doors may need to be modified)
- The need to check the strength of old ceramics before implementation
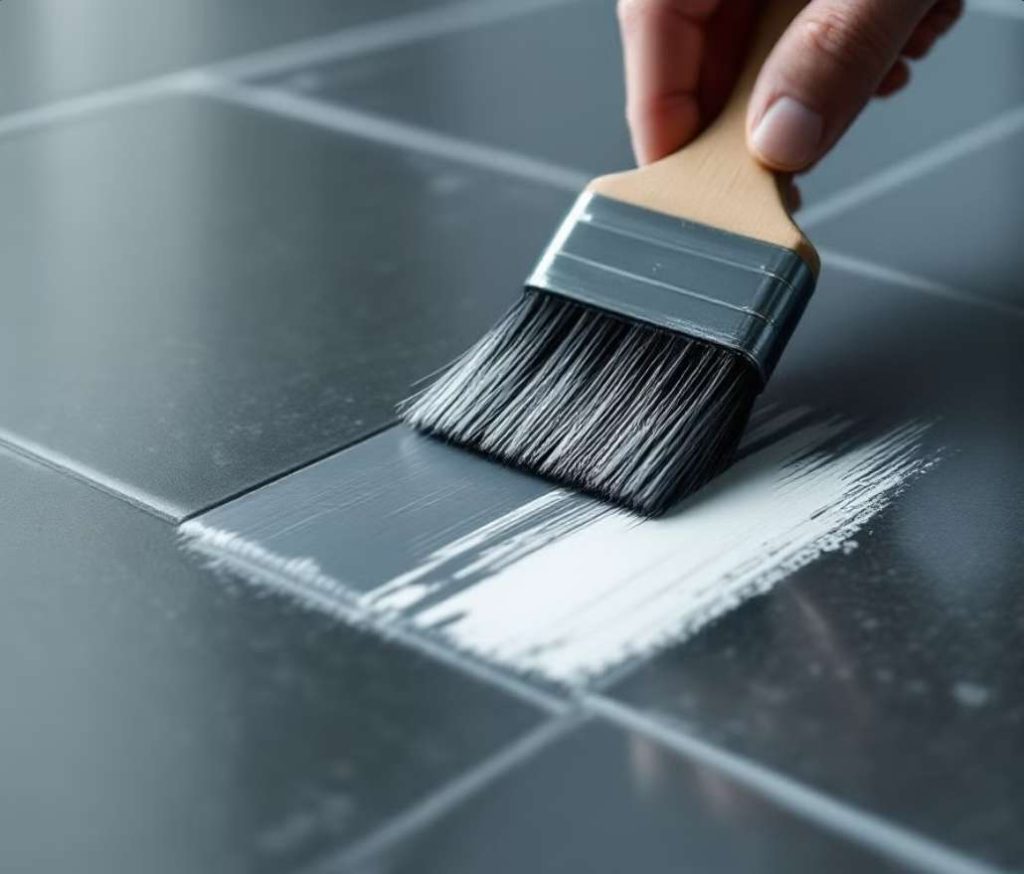
Checking the condition of the old floor before installing new ceramic
Before installing new ceramic, it is essential to check the condition of the old flooring:
- Check the strength of old ceramics: If there are loose tiles, they should be fixed or replaced.
- Evenness of the floor surface: If the surface is uneven, you may need leveling layers.
- Moisture resistance: If the previous flooring is exposed to high humidity, the use of waterproof adhesives is recommended.
Choosing the best type of ceramic for installation over old floors
- Ultra-thin ceramics: suitable for reducing floor height increases
- Porcelain ceramics: highly resistant to abrasion and moisture
- Anti-slip ceramics: suitable for wet environments such as bathrooms
Tools and materials needed to replace ceramics without destruction
- Tile adhesive on tile
- Spatula and comb for adhesive
- New ceramics
- Laser leveling device
- Suitable jointing mortar
Steps for replacing ceramic tiles without destruction (step by step)
- Cleaning and preparing the old surface
- Applying special adhesive
- Placing new ceramics and adjusting them
- Using a leveling device
- Performing grouting and final cleaning
Reviewing possible challenges and how to resolve them
- Challenge: Increasing floor height
- Solution: Using ultra-thin ceramics
- Challenge: Looseness of old ceramics
- Solution: Stabilizing and repairing damaged parts
How to maintain and increase the durability of new ceramics
After installing new ceramic tiles over old flooring, it is important to maintain them properly. Following a few simple tips can help preserve the durability and beauty of your ceramic tiles for years to come.
1- Regular cleaning and use of appropriate detergents
To clean new ceramics, use special tile and ceramic cleaners.
Strong acidic substances, such as salt ink or chlorine bleach, may damage the protective layer of ceramic.
2- Using resistant sealant and tape
To prevent water and moisture from penetrating, seal the ceramic joints well.
Every few years, inspect the seals and repair them if necessary.
3- Preventing impacts and scratches
When moving heavy items, use protective pads under furniture legs.
Avoid dragging sharp and metal objects over the ceramic.
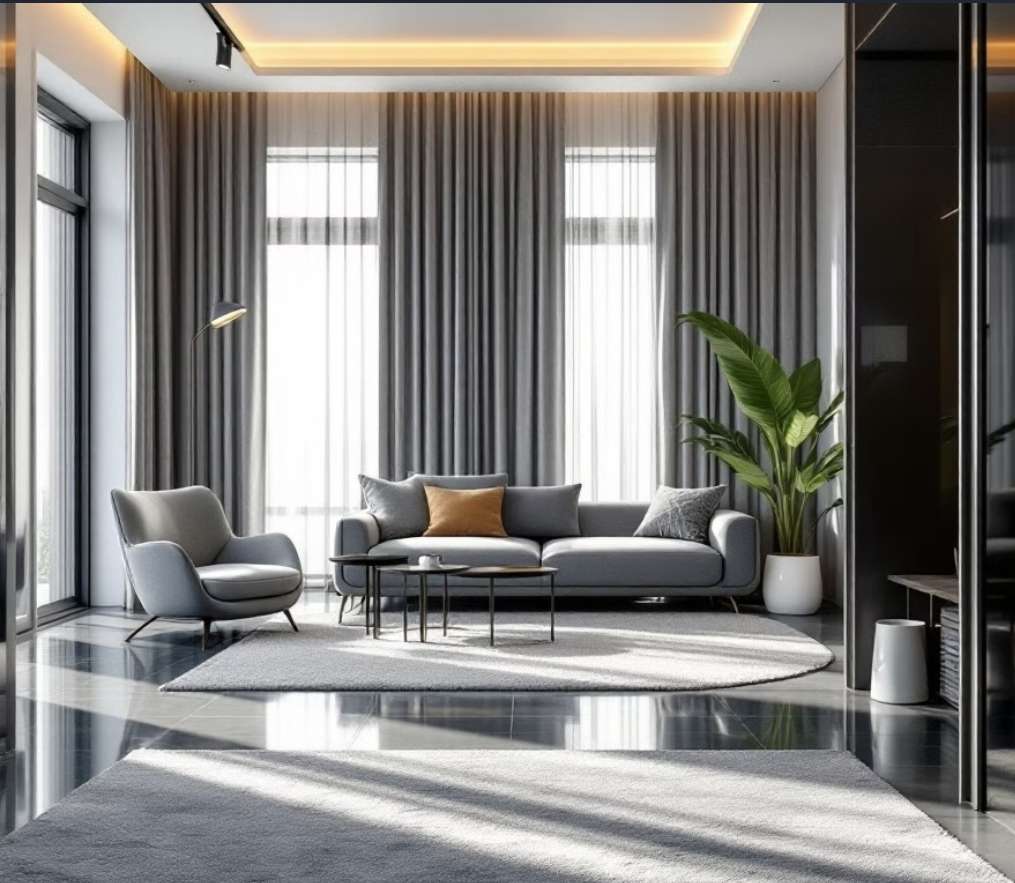
Is this method suitable for all spaces? (Review specific cases)
Replacing ceramic tiles without demolition is an excellent option for many spaces, but some environments have specific conditions that must be considered.
1- Apartments and Residential Buildings
This method is ideal for apartments, as demolition and dust creation can be problematic in such settings.
2- Commercial and Office Spaces
The quick application of this method helps reduce downtime and business disruption.
If there is high foot traffic, it’s important to use durable tiles like porcelain.
3- Wet Areas like Bathrooms and Kitchens
If the existing floor has moisture issues, special waterproof adhesives should be used.
Non-slip tiles are a suitable choice for these areas.
4- Industrial or High-Traffic Areas
In spaces where there is heavy weight and pressure on the floor, this method may not be durable enough.
In such cases, it’s better to opt for traditional methods or resistant industrial flooring.
Comparison of ceramic replacement costs: traditional method and non-destructive method
To better understand the cost differences, let’s examine each influencing factor separately:
1- Material Costs
Traditional Method: Requires purchasing mortar, adhesive, subfloor preparation, and new tiles.
Non-Demolition Method: Only requires new tiles and special adhesive, though in some cases, ultra-thin tiles, which are more expensive, may be needed.
Conclusion: Material costs are similar in both methods, but in the non-demolition method, special types of tiles might be required, which can increase costs.
2- Labor Costs
Traditional Method: Includes costs for demolition, subfloor work, installation, and grouting, which are time-consuming and expensive.
Non-Demolition Method: Only includes the cost of installing new tiles and grouting, which takes significantly less time.
Conclusion: Labor costs are lower with the non-demolition method because execution time is reduced.
3- Execution Time Costs
Traditional Method: Depending on the level of demolition and subflooring, it can take several days to several weeks.
Non-Demolition Method: Usually completed within one or two days.
Conclusion: The non-demolition method is significantly faster, which can reduce indirect costs such as business downtime or temporary relocation of residents.
4- Additional Costs (Debris Removal and Dust)
Traditional Method: Includes costs for removal of construction debris and post-demolition cleaning.
Non-Demolition Method: Due to the lack of demolition, there are almost no additional costs.
Conclusion: The non-demolition method not only reduces transportation costs for debris but also minimizes pollution and dust.
Summary:
If your goal is to reduce labor costs, increase speed, and avoid demolition, the non-demolition method is the better choice.
If there are height constraints on the floor or a need for subfloor modifications, the traditional method may be the better option.
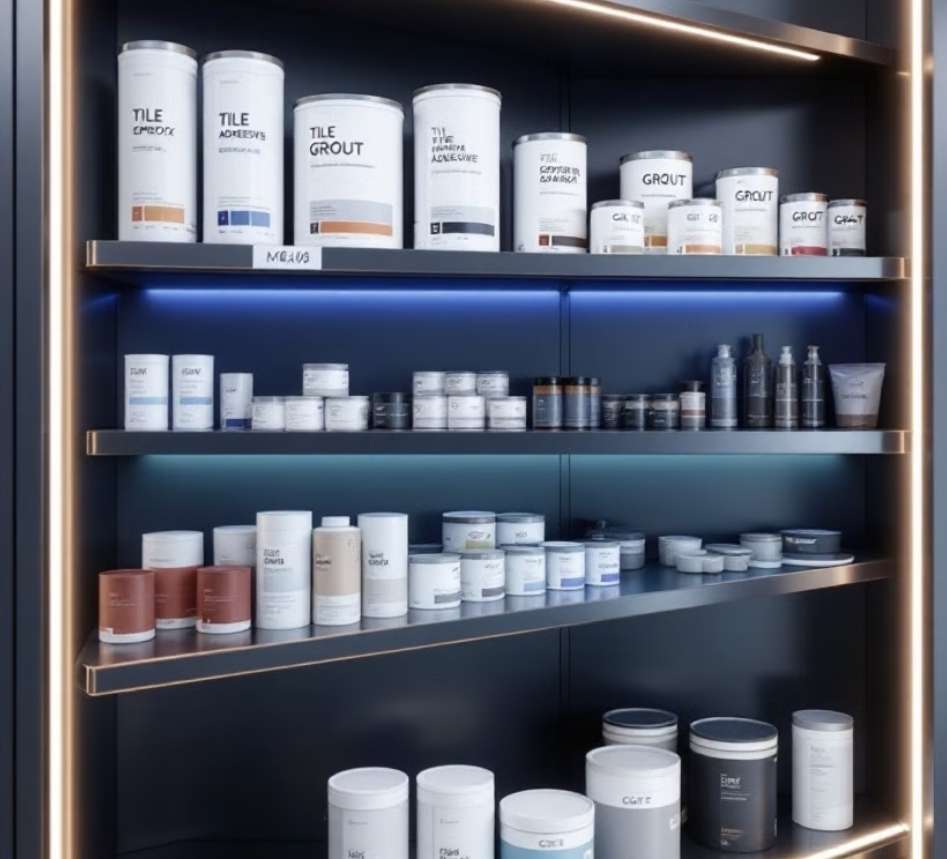
User comments and experiences: Has this method been successful?
To evaluate the performance of this method, we reviewed user feedback and experiences from individuals who have used it.
1- Satisfaction with Time and Cost Reduction
Most users were satisfied with the fast execution and reduced costs.
2- Concerns About Increased Floor Height
Some users reported that the increased floor height became problematic, requiring door adjustments.
3- Experience in High-Traffic Areas
In low-traffic environments such as homes and office spaces, this method performed well.
Some users in high-traffic areas observed a reduction in tile adhesion over time.
Conclusion: This method has been successful for most users, but in very high-traffic areas, it requires further evaluation.
Frequently asked questions about replacing ceramic tiles without damaging them
1- Can new tiles be installed over any type of existing tile?
Yes, but the underlying surface must be clean, solid, and free of deep cracks.
2- Is this method suitable for wet environments?
Yes, as long as special waterproof adhesives are used.
3- How much does the floor height increase?
Typically 5 to 10 millimeters, depending on the tile thickness and the amount of adhesive used.
4- Can this method be applied over wooden or laminate floors?
No, this method is only suitable for installation over ceramic, stone, or concrete surfaces.
Conclusion: Is non-destructive ceramic replacement right for you?
The main advantages of this method:
- Reduce execution time
- Reducing labor and material costs
- Preventing environmental destruction and pollution
Limitations of this method:
- Slight increase in floor height
- Need to check the strength of the previous floor
In conclusion, if your current flooring is in good condition and structurally sound, this method is the best way to update your floor’s design.
By choosing the right type of tile and ensuring proper installation, you can achieve a beautiful new floor without demolition.
We hope this guide helps you make a better decision. Do you have any experience in this field? Share your thoughts with us!
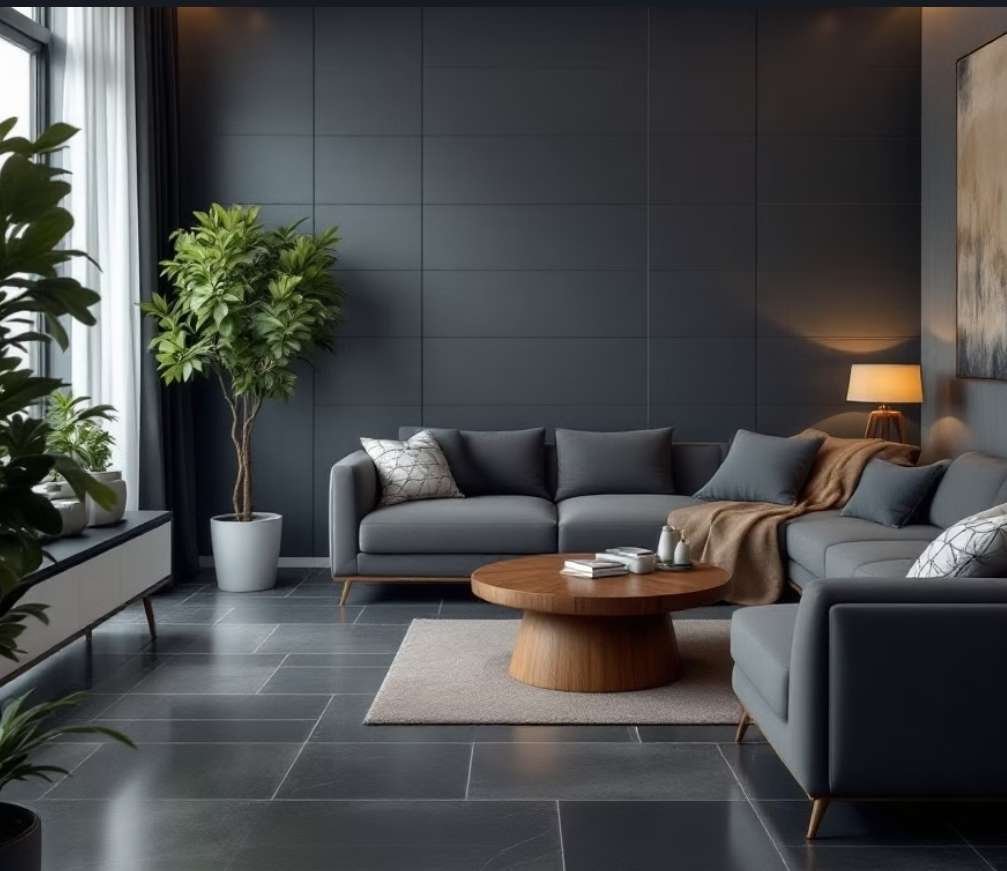